Pellet mill die and roller design and manufacturer
Roller and die is the core part of the pellet machine. They determines the forming rate and pellet quality. They are also the most wearable parts. This article introduces the design of roller and die in 2 types of pellet machine. TICO is a professional flat die pellet machine manufacturer in China. We supply roller, flat die and other spare parts for the pellet machine.
Flat die in pellet machine
In flat die pellet machine, the die is a disc with many holes on it. It is made of ductile cast iron. After carburizing and quenching treatment, the hardness is 55-60HRC. The size of the holes are from 2.5mm to 10mm. The most popular sizes are 6mm, 8mm and 10mm. To adapt to different materials and production requirement, the thickness and hole sizes are different.
The working life of a flat die is 300-500 hours. When one side has worn out, it can be used with the other side. The length and size of the hole is designed based on a large number of experiments, so that it achieves the best compression ratio for 30 biomass materials.
The flat die need to be replaced when it wears out. It doesn’t take much efforts. Just loosen the lock nuts on both sides, remove the upper chassis and take out the roller and flat die. TICO provides superior spare parts for the pellet machine, including roller and die.

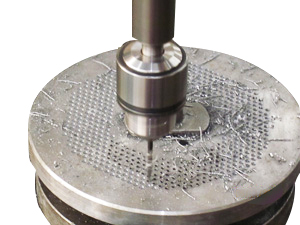
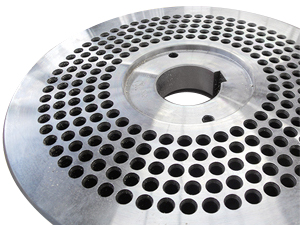
Roller in flat die pellet machine
In flat die pellet machine, the rollers are installed on the main shaft. 2 or more rollers are connected by a roller shaft. The rollers are cylinders with many skid-proof ace on its surface. During working, the roller shaft rotates around the main shaft, and the rollers rotate around the main shaft at the same time. The diameters of the rollers vary with the production capacity.
The hardness of rollers is lower than that of flat die, so that they reduce the wear on flat die, and prolong their working life. All rollers should have the same clearance with the flat die to achieve uniform pressure. The clearance is between 0.1-0.3mm.
The roller adopts tapered shape to ensure the rotating speed at the 2 ends are the same. This design can avoid slipping of the roller, reduce energy waste, and reduce the wear of flat die. Besides, it adopts an screw central pressure adjustment device. It allows you to adjust the clearance between roller and die, so as to adapt to different materials and ensure molding effect.
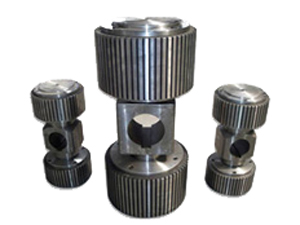
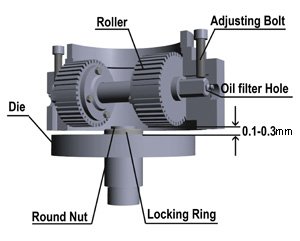
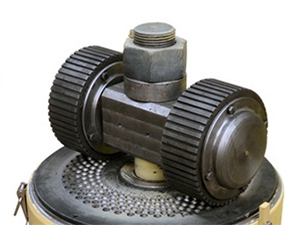
How do the roller and flat die work?
When the raw materials are fed into the pellet machine through the hopper. They fall on the flat die and roller. The roller rotates driven by the main shaft, and distribute the raw materials on the flat die evenly. During rotating, the roller and flat die forms strong pressure and fraction, which will heat up the compression chamber to 80℃. In this condition, the materials become soften and easy to mold.
The downward pressure from the roller squeeze the raw materials into the holes on flat die, in which they are formed into cylindrical strips. The strips become longer and longer as the roller keep squeezing the raw materials. When the strips come out from the bottom of the holes, there is a slicer cutting them off. The cut strips fall down and discharge from the outlet. These strips are what we call “wood pellets”.
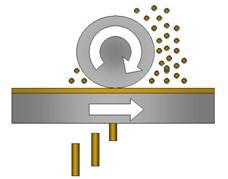
Flat die and ring die pellet mill comparison
Flat die pellet machine is suitable for home use and small workshop production. It costs low. The size is small and the production is relatively low. For large scale production, ring die pellet machine has more advantages. It has large production capacity and low power consumption, but the size and cost is much larger. The major difference between ring die and flat die pellet machine are the shape of the dies and the position of rollers.
Ring die in pellet machine
Ring die is an annulus with many holes on it. It is made of carbon steel (alloy steel) and stainless steel, and processed by forge and stamp, cutting, drilling and heat treatment. The strength of the ring die is influenced by the number of holes. The larger the size of holes, the less the number.
Rollers in ring die pellet machine
The rollers of ring die pellet machine are usually made of high-carbon steel or chilled cast iron. It should has higher hardness than the ring die, so that it can realize the best compression effect and uniform abrasion. The suitable clearance between the rollers and ring die is 0.1-0.4mm. There are axial grooves on the surface of the roller to grab the raw materials.
How do the roller and ring die work?
In ring die pellet machine, the 2 rollers are installed inside the ring die. The roller put pressure outward on the inner wall of the ring die.
The raw materials were first fed into the conditioner for blending. Then they are conveyed to the compression chamber by a screw feeder. In the compression chamber, the rollers are still and the ring die rotates drive by the electric motor. As long as the raw materials are grabbed by the ring die, they are squeezed into the holes. The high temperature and pressure cause physical and chemical changes to the raw materials. When they are extruded out from the ring die, there are slicers that cut them off. And the pellets falls down and get out through the outlet.
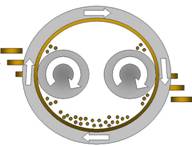
We receive enquiries in English, Español (Spanish), Русский язык (Russian), Français (French) and العربية (Arabic). Our professional team will reply to you within one business day. Please feel free to contact us!