How to use and maintain wood pellet machine properly?
Grinding before using
Most roller and flat dies in pellet machine are processed by high-heat treatment. After planing, drilling, milling, and quenching process, there are usually many rags inside the die holes, which may influence the pelletizing effects and production. Therefore, before starting a new pellet machine, or after replacing a new die, you need to grind it thoroughly.
We use oil mixture to process grind the roller and flat die. The oil mixture is composed of 20% fine sand, 65% biomass materials(like sawdust), 15% waste engine oil. Before feeding the oil mixture to the pellet machine, you should adjust the clearance between roller and flat die to 0.1-0.3mm. The grinding process should last 15-40 min.
For ring die pellet mill, the grinding process requires more oil mixture and longer time. The quantity of oil mixture is 10% that of pellet production per hour. The grinding time is 30-50 min. And the clearance between ring die and the roller is 0.1-0.4mm.
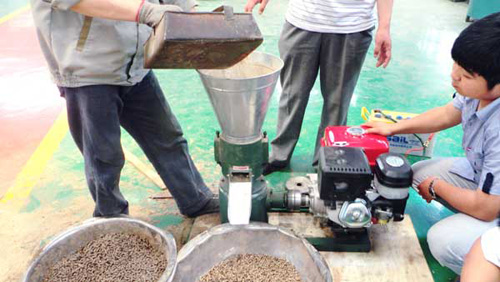
Pretreatment of raw materials
The suitable moisture content of biomass materials should between 14% and 20%. Dry materials are hard to take shape, damp materials will make the pellets loose. The size of the raw materials should be less than the hole size of pellet mill dies. Generally, the hole size of the pellet mill die is 6mm and 8mm, and the size of raw materials should be under 5mm, or they may block the holes and reduce pellet production.
The adhesive force determines the forming rate of the pellets. Most biomass materials contain lignin, which would melt under high temperature and serve as binder. But some materials like rice husk has low adhesive force. It need to be mixed with sawdust or binders to make pellets.
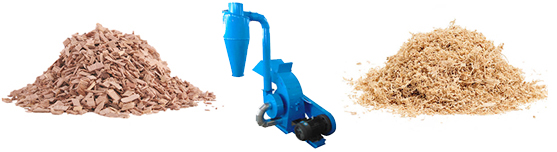
a hammer mill can crush the wood materials into small size
The thickness and length of the wood pellets
The thickness of wood pellets is determined by the hole size of the die. The length is determined by the slicer. In flat die pellet machine, the slicer is installed under the flat die, while in ring die pellet machine, the slicer is installed outside the ring die. Both of them can be adjusted to achieve different sizes. For your own use, it is better to be short. For transportation and selling, it recommend to be a little long.
After the wood pellets come out from the pellet machine, they are hot with some steams. They can be dried and cooled in an open field, or by a counter-flow cooler. Quick cooling can improve the hardness of the wood pellets, and facilitate storage and transportation.
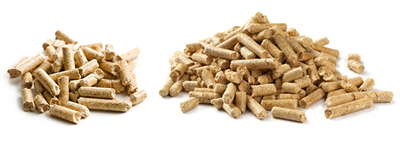
Don’t shut down the machine right after making pellets
When you finished making pellets, don’t shut the pellet machine down at once. Add some mixed oil and biomass materials to the pellet machine and let it run for 1-2 min. In this way, we can fill the die holes with oil mixture, so that we can directly start making pellets the next time. With this process, we can not only maintain the mold, but also save time. When the pellet machine stops, loosen the adjusting screw and clear away the left materials.
The maintenance of roller, die, shafts and gearbox
You should eliminate all hard objects and metal blocks in raw materials before feeding them into the pellet machine, or they would cause damage to the roller, die or main shaft. You can install a tubular magnet on the feed hopper.
The heat inside the pelletizing chamber can reach up to 80℃, and the roller sustains high pressure during operation. As there is no dust protector in the pellet machine, so you need to clean up the bearing every 2-5 hours, and lubricate it with oil. After every 8 working hours, the main shaft need to be oiled. The gearbox need cleaning every half a year. If there is abnormal high heat in the gearbox, you can use better gear oil and increase the clearance between the gears for maintenance. The fastening screw in the transmission part also need to be replaced regularly.
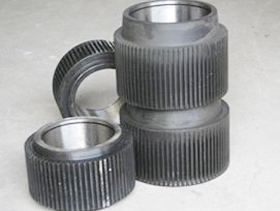
roller shell
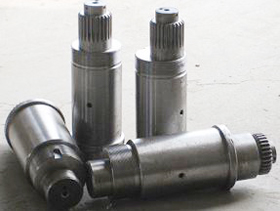
eccentric shaft
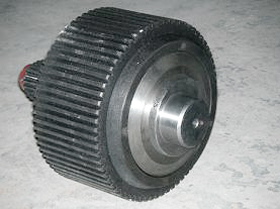
Roller
How to replace roller and die?
When the rollers wears out, you can replace the roller shell or the whole set of roller. If the bearing get loose or locked, you need to replace the bearing and even the shaft.
In ring die pellet machine, just loosen the hoop chuck, take the old ring die apart and replace it with a new one. If the ring die is fixed with screws, you need to shake the ring die gently, and remove the screw with even strength.
In flat die pellet machine, the flat die is installed with retaining nuts in the keyway. On the 2 sides of the flat die, there are two symmetrical screw holes. You can use the screw driver to push them out, or use a magnet to pull them out. During your pushing or pulling, keep the flat die vibrating with a hammer, so that the screw won’t stuck in the screw hole.
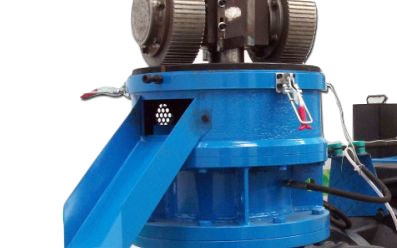
Protection of the drive engine
Choose the matched power according to the required production. If the power is not enough, the production will be low and the pelletizing effect is poor. If the power is too large, it will consume more power, accelerate the weariness, and shorten the service life of roller and die.
The exam and repair should be carried out in power off condition. The machine should be placed near the working place, so as to reduce the moving time as much as possible. Protect it from water logging, rain, electric leakage, fire, etc.
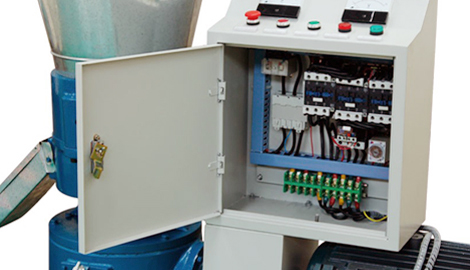
Only when we use the pellet machine properly and maintain it regularly can we take full advantages of the pellet machine and prolong its working life. TICO is a professional wood pellet machine manufacturer. Our products adopts superior materials and scientific design. Following our instruction and recommendation, you can make more profits from it.
We receive enquiries in English, Español (Spanish), Русский язык (Russian), Français (French) and العربية (Arabic). Our professional team will reply to you within one business day. Please feel free to contact us!