Measures to Keep the Best Performance of Biomass Pellet Mill
Maintaining the best performance of biomass pellet mill is to maximize the interests of users investing in biomass pellet mill industry. How to maintain the best performance of biomass pellet mill?
What are the specific measures?
Raw material control
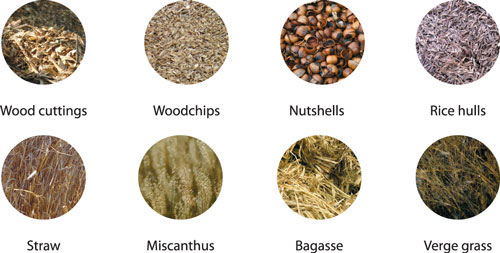
- Choose suitable raw materials to ensure the fineness of raw materials and feed uniformity.
- Rationality and effectiveness of iron removal device. Reduce the metals and impurities in raw materials.
- The moisture content of raw materials is the basic guarantee for the best performance of biomass pellet mill.
Rational matching of roller and die
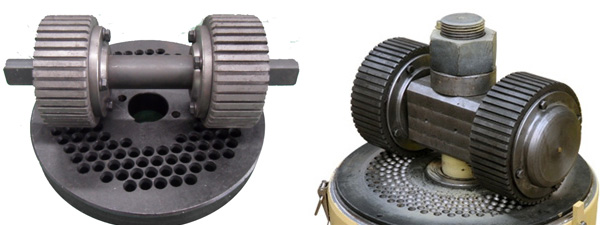
Choose stainless steel die, with wear-resistant material alloy roller. This is to restrict the biomass pellet mill from the material of the fragile parts. According to the material composition, the appropriate die compression ratio is selected to adjust the production gap between the die and the roller in the best state. Ensure the heat treatment uniformity and hardness of the roller. In the production process of biomass pellet mill, the replacement policy of die and roller must be observed, which is new to the new and old to the old.
Stability and persistence of biomass pellet mill
Appropriate current, timely maintenance, reasonable oil injection, moderate cooling, auxiliary equipment collocation and so on are the basic guarantee for the best operation.
Reasonable staffing arrangements
Reasonable personnel arrangement and operator selection are also prerequisites for optimum performance of biomass pellet mill.
Of course, the most important thing is to choose the right quality biomass pellet mill. Keeping the best performance of biomass pellet mill, sawdust pellet mill, fuel pellet mill and bark pellet mill can make the industry go further.
We receive enquiries in English, Español (Spanish), Русский язык (Russian), Français (French) and العربية (Arabic). Our professional team will reply to you within one business day. Please feel free to contact us!