What affect the molding effect of biomass pellets?
Biomass energy has many application modes, such as biogas, alcohol, and biomass molding fuel. Biomass molding fuel is the most convenient and economical mode. Biomass molding fuel has biomass pellets and biomass briquettes 2 forms. Biomass pellets gradually replace briquettes owing to small size, high density, and easy use.
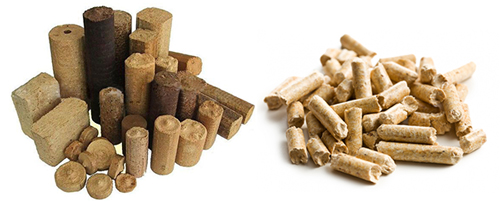
Biomass briquettes and biomass pellets
Biomass pellets are made of wood pellet machine. It uses high pressure from roller and die to mold biomass materials into high-density solid pellets. The molding effect is influenced by the raw material quality, molding process, and equipment performance. To improve the molding effects of biomass pellets, you should learn about the following factors.
Raw material quality
Raw material composition
The raw materials for making wood pellets are composed of different contents. They have different reactions in high heat and high pressure. Some contents like proteins and lignin will soften and have gluing effect. Some contents like cellulose and inorganic particles are hard to break down or split. They hinder the molding of wood pellets, but they takes up the most part of biomass materials.
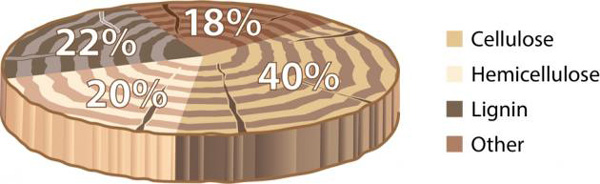
The composition of raw materials has the largest influence on the pellet durability. The following chart shows the Pellet Quality Coefficient (PQF) of several common raw materials.
biomass material | PQF | biomass material | PQF | biomass material | PQF |
---|---|---|---|---|---|
Barley | 5 | Acid oil | -40 | rapeseed cake | 5.5 |
bentonite | 10 | soybean meal | 4 | feed mill leftovers | 3.5 |
dried blood | 3 | feed materials | 9 | Sorghum | 3 |
Whey Powder | 2 | fish meal | 4 | oats | 7 |
molasses | 5.5 | limestone | 5xiao | wheat meal | 8 |
wheat | 7 | minerals and vitamins | 3 | beans lignin | 50 |
The larger the PQF, the tighter the wood pellets are bound. Some materials like bentonite, lignin have high PQF. They can serve as binders. Some materials like acid oil has low PQF, the particles inside can’t bind together effectively. Loose biomass pellets has less durability. Only when the total PQF of all materials add up to more than 4.7, the wood pellets can take shape successfully.
The fineness of raw materials
Raw materials with smaller granularity have larger surface area, so they are easy to bind. And the produced pellets are more compact and smooth, not easy to break. The smaller the granulates, the higher the wood pellet strength. But too small granulates requires high energy consumption for pulverizing. It is not recommend to pursue too small granulates.
The granulates should be uniform in size. Too large granulates are not easy to bind with others, and the surface tend to be rough. Large particles usually cause radiant crack, where the wood pellets are easy to break. Too large granulates are hard to get into the die holes. They will aggravate the abrasion of pellet mill die and roller, reduce the wood pellet production, and lower the molding rate.
Therefore, the granularity of raw materials should be 1/2-2/3 of the wood pellet size. You can adopt a screener with the pore diameter less than 10mm in pulverizing process, so that the raw materials can meet the standard for pelletizing and mixing, and reduce the power consumption and equipment abrasion.
The moisture of raw materials
The moisture in the biomass materials have lubrication function. They can reduce the friction between the granulates, and enhance their bonding. The moisture can also soften the materials so that they are easier to deform and mold.
Biomass materials varies in moisture content, usually between 8%-15%. The moisture is affected by temperature. For those materials with over-high moisture, we need to dry them before making pellets.
Molding process
The molding temperature
The biomass molding is to make the organic parts of biomass soften, bond and transformed under high temperature and pressure.
Usually, the organic matters soften at the temperature of 70℃~80℃, bond at the temperature of 160℃, liquefy at the temperature of 240℃. With the increase temperature, the raw materials become more soften, the liquidity increases, the resistance between raw materials decrease, so they are easier to mold. As measured, the molding pressure in high temperature is half of that in high temperature.
High temperature is not always good. Over-high temperature will cause carbonization of the biomass materials. Such carbonization is neither uniform nor controllable, which will hinder molding and affect the wood pellet quality.
The thickness of material layer
In pellet machines, there is a clearance between the roller and die, where the biomass materials form a layer. The clearance can be adjusted from 0.1mm to 0.3mm. To produce small-size wood pellets, the clearance is small, and vice versa.
The thickness of material layer also influence the power consumption of the pellet machine. When the material layer is thick, the extrusion pressure will increase. With too much raw materials getting into the die holes, they will be too tight to discharge, and even cause damage to the equipment. When the material layer is too thin, the extrusion pressure is small, the raw materials squeezed into the die holes are insufficient, so the wood pellet production is low.
The picture below shows the influence of raw materials on the extrusion force. B refers to suitable thickness, A refers to the layer is too thick, C refers to the layer is too thin. In the A status, the extrusion force increase a lot owing to the long squeezing area. In the C status, the extrusion force is too small. So a suitable thickness is a premise of high-efficient production.
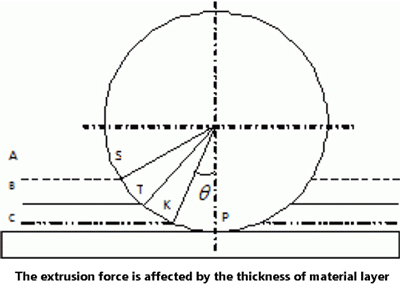
Equipment performance
Extrusion speed
Extrusion speed determines the time that raw materials are in the die holes, so as to affect the molding quality. When the raw materials leave in the die holes for short time, the unit power consumption is low, but the wood pellets may be loose. When the raw materials leave in the die holes for long, the wood pellets will have higher density and quality, the unit power consumption also increase.
If the raw materials leave in the die holes for too long, the friction will be too high, the pellets will be too dense, the pellet machine will be hot and even stop.
The extrusion speed of a pellet machine is affected by the roller diameter and rotating speed. A proper extrusion speed ensure the equipment work continuously with low power consumption.
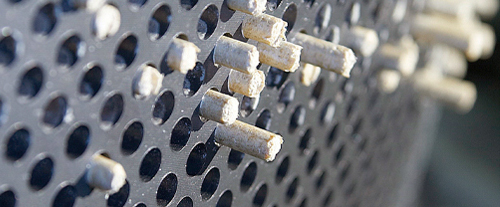
Extrusion strength
The squeezing pressure on the raw materials determines the density of wood pellets. High pressure extrusion and friction will soften and deform the raw materials and bind them together.
If the extrusion strength is insufficient, the raw materials can't be molded successfully. If the extrusion strength is too high, it will aggravate the abrasion of dies and add to cost.
The parameters of die hole
The parameters of die holes are restricted by raw material granularity, extrusion speed, extruding strength. Oppositely, the parameters of die holes influence the molding of wood pellets.
Pellet mill die holes have certain compression ratio. High compression ratio increase the extrusion strength, lower the extrusion speed. They are suitable for the materials with low adhesive force.
The hole entry shape influence the speed of raw materials getting into the die holes, and influence the thickness of raw materials.
The parameter of die holes should be adjusted according to different materials, so that you can get high-quality wood pellets with low unit power consumption.
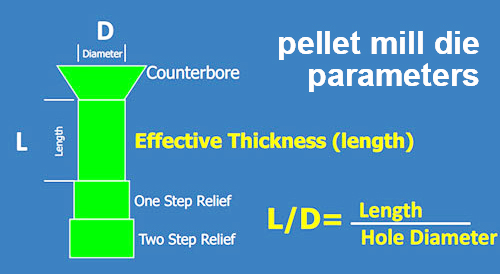
We receive enquiries in English, Español (Spanish), Русский язык (Russian), Français (French) and العربية (Arabic). Our professional team will reply to you within one business day. Please feel free to contact us!