Biomass fuel molding equipment and technology
What is biomass molding fuel?
Biomass molding fuel is called BMF in short. They are briquettes, bars, pellets compressed from agriculture and forestry wastes. The production process of biomass fuel includes: raw material collection, crushing, blending, drying, molding, discharge, cooling and packing. The molding process is carried out by specialized biomass equipment. Biomass molding fuel has high heat value and low pollutant emission, so it is an ideal substitute for fossil fuel.
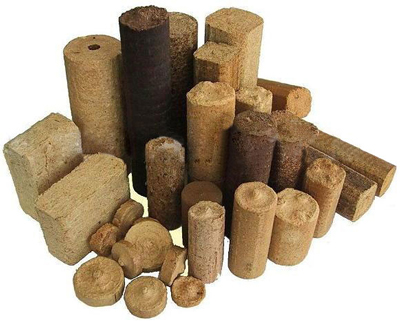
How are biomass fuels made?
Biomass molding refers to compressing dry and crushed agriculture wastes into compact and solid briquettes or pellets. As the biomass materials contains high lignin content, it will melt under high temperature and serve as binders that glue the materials together. Sometimes they need to be added with some binders or additives. The biomass molding equipment has the processes of crushing, hot molding and shape maintenance.
The compressed biomass fuels are used in heating stove, industrial boiler and power plant. They have the advantages of high density, good burning performance, high heating efficiency, low ash residue, and low pollutant emission. Besides, they are easy to ignite, store, and transport, with large market developing prospect.
Biomass fuel molding equipment
According to different molding technology, the biomass fuel molding equipment can be classified into 4 types: stamping briquette press, screw extruding briquette machine, ring die pellet machine, and flat die pellet machine.
Stamping briquette press
Stamping briquette press use the two-way squeeze of reciprocating pistons to mold biomass materials into briquettes. By replacing the extrusion mold, stamping briquette press can produce briquettes of different sizes and shapes. As stamping briquette press has short extrusion time, so the density of briquettes is relatively low.
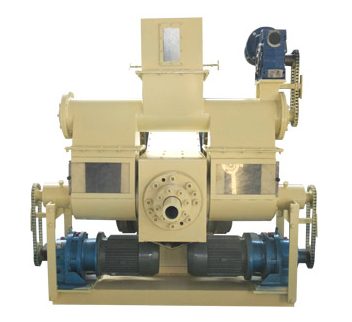
Screw extruding briquette press
Screw extruding briquette press has the similar structure as meat grinder. The molding structure includes a screw propeller, compression chamber, holes on molds, and a slicer. When the raw materials are fed to the briquette press, the screw propeller press them forward until they pass through the holes on the moulds, where they are formed into cylindrical bars. After that, the slicer cut the bars into certain length.
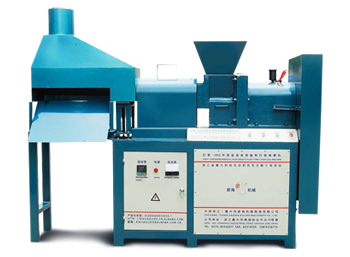
Ring die pellet machine
The molding part is a ring die with many holes on it, and 2 or 3 press roller inside the ring die. When the raw materials are fed to the compression chamber, the roller press the raw materials outward, and squeeze them into the holes on the ring die. When the raw materials pass through the holes and come out, they become solid cylindrical pellets. Then slicers cut them short. Ring die pellet machine has large capacity, suitable for medium and large wood pellet factory.
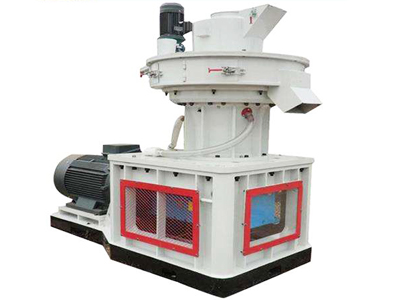
Flat die pellet machine
In flat die pellet machine, the roller is installed on a vertical shaft and cling to the upside of the flat die. The raw materials fall on the flat die and the roller press them downward. Then they are squeezed out from the holes on flat die and cut by a slicer. Flat die pellet machine has smaller size and low cost, suitable for home use and small wood pellet factory.
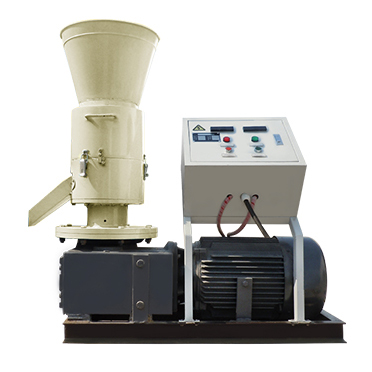
Requirement on materials to make molding fuel
Small size and high density
The higher the density and fluidity of raw materials, the higher the production. The suitable size of raw materials is under 5mm. It is recommended to crush the crop straws into fine granules with a wood pulverizer. If you use a knead machine to process the raw materials, there will be many silks, which is hard to feed, and the production is low.
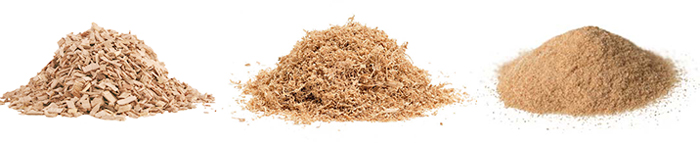
Proper water content
The suitable moisture content of raw materials should be 15%-18%. Too high or too low water content will both influence the production and quality of biomass fuel. If the moisture content is too high, the raw material will cause slipping between the inner wall and moulds, and even block the mould. If the moisture content is lower than 14%, the raw material will cause severe friction to the moulds, and the production is low.
We receive enquiries in English, Español (Spanish), Русский язык (Russian), Français (French) and العربية (Arabic). Our professional team will reply to you within one business day. Please feel free to contact us!